지원사업우수사례
명성티엔에스(주)
우수사례 선정년도 | 2018년도 | 지원사업명 | 산학연협력기술개발사업 |
---|---|---|---|
지원기간 | 2015. 5~2016. 6 | 과제명 | 리튬이차전지 분리막용 TDO설비의 클랩핑 두께 25um이하급 고배율 연신용 체인 베어링 클립 개발 |
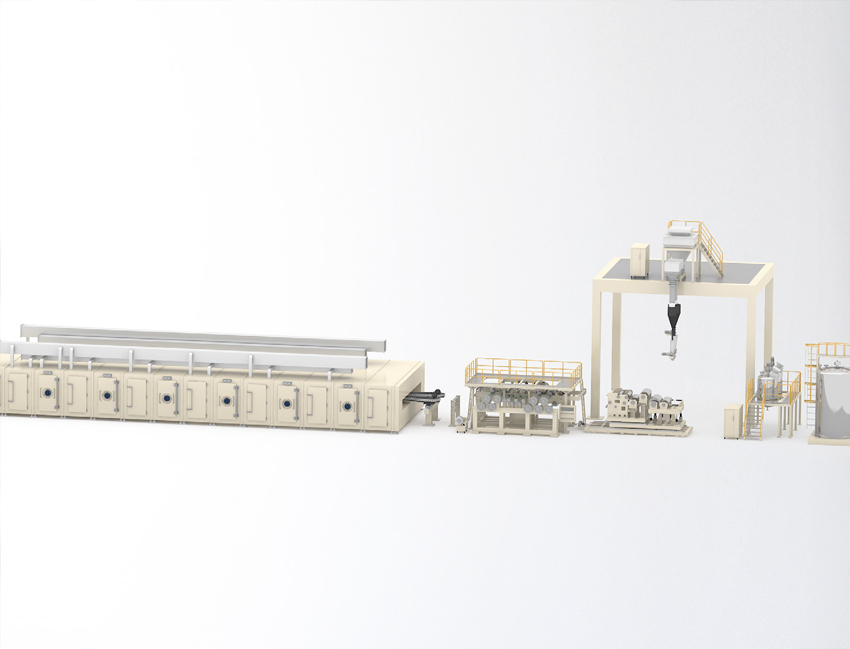
과학 분야에 흥미가 많은 중학생 김우주(가명) 군은 최근 청소년 과학 잡지를 통해 미 래 환경에너지로 꼽히는 이차전지 관련 기사를 접하게 되었다. 휴대폰, 노트북을 포함 해 최근 사용이 확대되고 있는 전기자동차까지 이차전지, 특히 리튬이차전지의 사용은 생각보다 생활에 밀접했다. 김 군의 파고들기 검색은 이차전지 제조에까지 이르렀는데 전지 안 양극과 음극을 분리하는 분리막이 대부분 해외 수입으로 조달되고 있다는 사 실에 적잖이 충격을 받았다. 그걸 만드는 기술과 기계가 국내에 없을까. 낙담하던 김 군은 검색 끝에 최근 코스닥에 상장한 명성티엔에스(주)를 알게 되었다. 이곳이 국내 최초 분리막 제조 설비 국산화에 성공한 곳이라는 걸 안 후 중소기업의 힘이 무엇인지 진정 깨닫게 되었다.
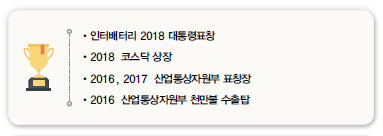
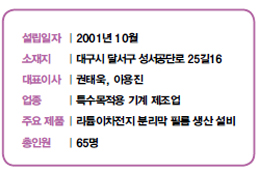
명성티엔에스(주)의 주력 제품이나
기술개발 배경은?
우리는 이차전지의 분리막 생산 장비 제조 업체다. 원천기술은 일본을 비롯한 외국이 갖고 있으나 거기에 우리 기술을 접목시켜서 2010년도 최초로 국산화에 성 공했다. 그 전엔 이차전지 생산 공정 중 일부를 담당하 고 있었는데 어느 날 전체를 만드는 회사가 없어져서 그 라인을 우리가 다 맡게 되었다. 축척된 기술과 노하우가 있어서 자연스럽게 흡수할 수 있었던 것이다. 또한 중 국시장에 진출하면서 일본이 가진 분리막 생산 장비는 우수한 반면 금액적으로 차이가 컸고, 또 우리는 분리 막 생산 이외 코팅 등의 가공 쪽을 함께 하면서 분리막 의 단가를 올려 경쟁력과 가치를 높이며 성장했다. 앞으 로 전기자동차 등을 포함해 분리막 시장이 엄청나게 커 질 전망이다. 최근에도 한 중국 업체와 재계약을 했는데 대단히 큰 규모다. 분리막 생산 시장에 들어오기 위해서 최소 500억에서 1천억 원이 들어가기에 쉽게 뛰어드는 회사가 없다. 따라서 우리 회사의 수출비중이 대단히 높 고 그만큼 경쟁력을 갖추고 있다고 볼 수 있다.
분리막 필름용 클립의 국산화 기술
개발과정은?
클립이라 하면 일상생활에서 종이에 꽂아 사용하는 것을 쉽게 생각할 수 있다. 분리막 제조 공정에서도 필름 양쪽을 클립으로 꽂아서 필름을 늘리고 줄이면서 만 들어간다. 그런데 필름을 집는 과정에서 클립의 강도라 든지, 굉장한 고열에서 진행되기에 열에 대한 내구성 등 이 대단히 중요하다. 과거 분리막 제조 기계를 만들 때 45억 비용 중 일본에서 사오는 클립 비용만 9억이 들 었다. 총 25%를 차지할 정도로 클립 비용이 컸던 셈이 다. 그 단가를 줄여보자는 생각에서 개발을 시작하게 되 었고, 본사에서는 장치의 설계 및 제작 기술을, 한국섬 유기계융합연구원에서는 구조 및 열 해석을 통한 형상 최적화 작업을 담당했다.
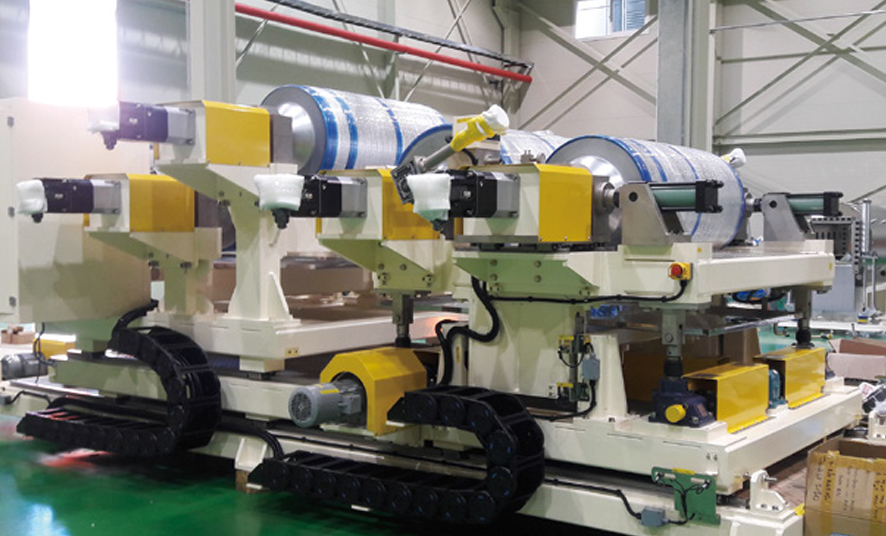
타 경쟁사에 비해 명성티엔에스(주)의
강점이 있다면?
한국섬유기계융합연구원과의 협업으로
인한 기술 개발의 특장점은 무엇인가?
명성티엔에스(주)의 향후 계획은?
[ 명성티엔에스(주)의 회사철학 ]
그릇이 작으면 작은 주문 밖에 못 받는다. 그릇을 키워두면 처음엔 막막할 수도 있지만 나중엔 결국 그 그릇이 다 채워진다. 우리 역시 창업 당시 섬유 기계 쪽을 했지만 이후 중공업 쪽 일도 했었고 담수 라인 일, 태양광 관련 일도 했었다. 당시 산업 환경 안에서 살아남을 수 있게 여러 가지 일을 하면서 기 술과 에너지가 축적이 된 것이다. 한쪽 방면만 하다 다른 걸 하려면 시간이 필요하고 그 기회를 놓치게 되는데 우리는 여러 가지 일들을 해오다 보니 기회 가 왔을 때 그걸 잡을 수 있는 그릇이 되었다.
2. 결국엔 사람이다
결국 사업 자체가 사람이라고 본다. 사람의 선택이 기회를 좌우하기 때문이다. 누군가 기술개발의 목적 이 있다면 회사에서도 관심을 기울여야 하고, 그런 사람이 나오기 위해 회사 역시 노력해야 한다. 같 이 하는 협력업체들도 생각하는데, 우리 회사로 인 해 먹고 사는 사람들이 몇 명인가를 생각하면 정신 이 번쩍 든다. 사람이 기업을 살리고, 기업이 사람 을 성장시키는 건강한 상생이 중요하다.
명성티엔에스(주)의 개발사업 성공 노하우
기술 개발 과정에서 100% 성공한다는 보장은 없다. 이 중 10%만 성공 해도 큰 이익을 보는 셈이라고 생각하는데, 나머지 90%의 실패를 통해 수많은 기술을 습득하게 되고 또 성공으로 가는 확률이 더 높아지기 때문 이다. 성공의 디딤돌이 바로 실패인 것이다. 어느 한 기술과 제품을 개발 했다고 단숨에 기업 매출이 오르는 게 아니다. 물론 그런 예는 10개 중 한 두 개 정도 있을 수는 있는데 나머지들은 미래를 위한 거름이 된다. 그 래서 도전하는 것이다. 현재 이슈인 분리막 관련 사업도 10여 년 전에 비 슷한 아이템을 내서 시행착오도 많이 했고 손해도 많이 봤었는데 그렇게 준비한 것을 계속 갖고 있다 보니 결국 성과를 내게 되었다.